联系我们
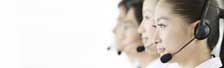
聊城开发区洪祥铸造加工厂
手机:13061508319
邮箱:996994159@qq.com
地址:山东省聊城市李海务蔡庄
- 公司动态
-
炉排及辅机安装调试工艺
发布时间:2015-06-26 18:02 来源:未知炉排及辅机安装调试工艺
一、炉排安装调试工艺
1.0适用范围
本工艺依据GB50273《工业锅炉安装工程施工及验收规范》、GB50231《机械设备安装工程施工及验收通用规范》要求制定。适用于组装或散装锅炉的炉排安装;而对快装锅炉,炉排出厂前已调试完毕与本体组合为一体,安装可参见吊装工艺。
2.0安装工艺流程
3.1人员:由相关工艺责任工程师负责技术指导,由焊工、起重工、管钳工、电工等工种配合组成施工队伍。
3.2技术准备:熟悉图纸,图纸会审,编制施工组织设计,由设计单位进行技术交底。
3.3施工机具及设备:根据施工组织设计、炉排的自重、尺寸和结构特点等技术数据选择合适的起重设备和机具进场,并对其进行全面性能检查
3.4会同有关单位代表,核对图纸、清单,对到场设备、材料进行验收,并填写设备《开箱检验记录》。
4.0 安装步骤
4.1基础验收:设备基础混凝土强度须达到设计要求,预留孔洞是否符合图纸要求,坐标、标高和几何尺寸符合以下规定,详见下表。
项 目 允许偏差 ㎜ 纵轴线和横轴线的坐标位置 ±20 不同平面的标高 -020 平面外形尺寸 ±20 平面水平度 不大于10㎜ 预留地脚螺栓孔中心位置 ±10
根据平面图位置在炉排基础上划出中心基准线,并对标高基准点进行标记。验收完毕后,填写《锅炉本体安装记录》。
4.3施工准备:
4.3.1安装前,清除基础表面和地脚螺栓孔内杂物。
4.3.2链条炉排安装前的检查项目和允许偏差符合下表规定
项 目 允许偏差 ㎜ 型钢构件的长度 ±5 型钢构件直线度 1(每米) 10(全长) 各链轮与轴线中点间的距离 ±2 同一轴上的任意两链轮,其齿尖前后错位△ 3
4.4.1按施工现场场地情况,按施工组织设计内容确定起重设备类型、设备进场路线、作业半径,选择合适锚固点,将炉排或主要部件起吊置于基础上。
4.4.2链条炉排安装时的允许偏差符合以下规定:
项 目 允许偏差 mm 中心位置 2 墙板的标高 ±5 墙板的垂直度、全高 3 前后轴的水平度 长度的1/1000 各道轨应在同一平面上,其平面度 5 相邻两道轨间的距离 ±2
4. 4. 4 炉排片组装不可过紧或过松,装好后应用手扳动,转动宜灵活。
4. 4. 5 边部炉条与墙板之间,应有膨胀间隙。
4.4.6往复炉排的允许偏差符合以下规定:
项 目 允许偏差 mm 两侧板间的相对标高 3 两侧板的垂直度、全高 3 两侧板间两对角线的长度之差 5
4.5 减速机安装:
4.5.1 将垫铁放在基础上,靠近地脚螺栓孔。
4.5.2 将减速机上好地脚螺栓,吊装到垫铁上,调整基准线的相对位置使其吻合。
4.5.3 根据炉排输入轴的位置和标高通过调整垫铁校正标高,同时尚需校正减速机输出轴和炉排输入轴之间的同心度和联轴器两端面的间隙。允许偏差按结构形式参照执行《机械设备安装工程施工及验收通用规范》中的有关规定。
4.5.4 减速机找平找正后,可对地脚螺栓孔灌注混凝土,捣实,达到70%以上强度时,拧紧地脚螺栓,并复核减速机的水平度。
4.5.5 暂不连接减速机和炉排输入端联轴器,检查减速机的油位,单独试车,检查电流等参数和各档位的运行情况,合格后填写《单机试运行记录》
4.6 燃烧器安装:
4.6.1燃烧器安装前的检查,应符合下列要求:
a 安装燃烧器的预留孔位置应正确,并应防止火焰直接冲刷周围的水冷壁管。
b 调风器喉口与油枪的同轴度应不大于3㎜。
c 油枪、喷嘴和混合器内部应清洁,无堵塞现象;油枪应无弯曲变形。
4.6.2燃烧器安装时,应符合下列要求:
a 燃烧器标高允许偏差为±5㎜。
b 各燃烧器之间的距离为允许偏差为±3㎜。
c 调风装置调节灵活。
4.7 冷态试运转
4.7.1 炉排冷态试运转宜在筑炉前进行,并应符合下列要求:
a 冷态试运转时间规定:链条炉排不少于8h,往复炉排不少于4h。试运转速度不应少于两级,在由低速到高速的调整阶段,应检查传动装置的保安机构动作。
b 炉排转动应平稳,无异常声响、卡住、抖动和跑偏等现象。
c 炉排片应能翻转自如,且无突起现象。
d 滚柱转动应灵活,与链轮啮合应平稳,无卡住现象。
e 润滑油和轴承的温度均应正常。
f 炉排拉紧装置应留适当的调节余量。
4.7.2 链条炉排挡渣铁(老鹰铁)应整齐地贴合在炉排面上,在炉排运转时不应有顶住、翻倒现象。
4.7.3 煤闸门及炉排轴承冷却装置应作通水检查,且无泄漏现象。
4.7.4 煤闸门升降应灵活,开度应符合设计要求。煤闸门下缘与炉排表面的距离偏差不应大于10mm。
4.7.5挡风门、炉排风管及其法兰结合处、各段风室、落灰门等均应平整、密封良好。
4.7.6侧密封块与炉排的间隙应符合设计要求,防止炉排卡住、漏煤和漏风。
4.7.7冷态试运行结束后应填好记录,甲乙双方签字。
二、辅 机 安 装 工 艺
1.0风机的安装
离心鼓引风机的清洗、拆卸和装配应符合下列要求:
1.1各机件和附属设备均应清洗干净,其接合面的防锈油脂除去后,应涂以润滑层加以保护(特殊要求者例外)。
1.2 机壳垂直中分面不应拆卸清洗(筒型结构的机器按设备技术文件的规定执行)。
1.3 润滑系统、密封系统中的油泵、过滤器、油冷却器和安全阀等应拆卸清洗,除油冷却器外其余均可不单独试压。
1.4 气体调节装置和气体冷却系统应拆洗干净,其受压部分一般可不进行试压;如有特殊要求者,应按设备技术文件的规定进行严密性试验。
2.0离心鼓引风机找平时,应符合下列要求:
2.1 直联机组找平时,纵向用水平仪在轴上测量,不水平度不应超过0.03/1000;横向用水平仪在机壳中分面上测量,不水平度不应超过0.1/1000;
2.2 有增速器的机组找平时,纵向用水平仪在轴颈上测量,不水平度不应超过0.02/1000;横向用水平仪在下机壳的水平中分面上测量(见图-2-1),不水平度不应超过0.1/1000;整个机组的找正一般均以增速器为基准进行。
3.1 接机组的大小选用成对斜垫铁,对转速超过3000转/分的机组,各块垫铁之间、垫铁与基础、底座之间的接触面积均不应小于接合面的70%,局部间隙不应大于0.05毫米;
3.2 每组垫铁选配后应成组放好,并作出标记防止错乱;
3.3底座如为数块组成者,应按设备技术文件的规定核对机壳和轴承座等地脚螺栓的位置是否相符。
3.4 底卒导向键(水平平键或垂直平键)与机体间的间隙应均匀,并符合设备技术文件的规定。如无规定时,键在装配的键槽内的过盈应为0.01-0.02毫米;在对应可滑动的键槽内两侧间隙的总和C1+C2应为0.04-0.08毫米;顶间隙C应为0.5-1.0毫米;埋头螺钉低于键a应为0.3-0.5毫米(见图-2-2)。
4.1 轴承座与下机壳为整体的机组,应将机体的下半部装在底座上,同时以轴承孔为基准,找平(有增速器的机组一般以增速器为基准进行上述工作)。
4.2轴承座与下机壳不是一体的机组,轴承座应先装在底座上,同时以轴承孔为基准找平,校正下机壳与主轴轴心线的不同轴度(有增速 器的机组,一般以增速器为基准进行上述工作)。
4.3有导向键的轴承座或下机壳上的锚爪与底座相连接的螺栓应正确固定,螺栓与螺孔间均间隙和螺母与机座间的间隙,应符合设备技术文件的规定;无规定时,螺母与机座间的间隙C一般可为0.03-0.06毫米(见图-2-3)。
注:机座指轴承或下机壳的锚爪。
5.0增速器底面与底座应紧密贴合,未拧紧螺栓前用塞尺检查其局部间隙不应大于0.04毫米。
6.0轴瓦与轴颈的接触弧面、顶间隙、侧间隙均应符合设备技术文件的规定。如某项指标不符,允许进行修、刮;但修、刮轴瓦时,应注意校正转子与机壳密封装置的不同轴度,并使转子与密封装置间的间隙符合设备技术文件的规定(可倾瓦轴承应符合设备技术文件的规定)。
7.0转子各部位(主轴、叶轮、平衡盘、推力盘和联轴器等)的轴向和径向跳动均不应超过设备技术文件的规定。
8.0上、下机壳的接合面应紧密,未拧紧螺栓前,局部间隙允许值应符合设备技术文件的规定,无规定时,应符合下列要求:
8.1 工作压力低于或等于1.0MPa,间隙不应大于0.12毫米(烧结鼓风机例外);工作压力高于1.0MPa/平方厘米者,间隙不应大于0.08毫米。
8.2 连接螺栓不应碰伤,接合面间如有密封填料或涂料应按设备技术文件 规定均匀地填上或涂上。
9.0增速器组装时,应符合下列要求(行星齿轮增速器按设备技术文件的规定执行);
9.1轴瓦的各部间隙、接角弧面和单位面积内的接触点数,应符合设备技术文件的规定,必要时应进行刮研;
9.2齿轮组轴间的中心距、不平行度、齿侧间隙和接触斑点应符合设备技术文件的规定。
9.3齿轮箱的上、下壳体接合面应紧密,未拧紧螺栓前其局部间隙不应大于0.06毫米,连接螺栓不应碰伤。
10.0所有上瓦背与轴承盖(或压盖)的过盈值以及下瓦背和轴承孔的接触面均应符合设备技术文件的规定;无规定时,过盈值一般应为0.03-0.07毫米,接触面一般不应小于75%。
11.0风机试运转应分两步:第一步机械性能试运转;第二步设计负荷试运转。一般均应以空气为压缩介质,风机的设计工作介质的比重小于空气时,应计算以空气进行试运转时所需的功率和压缩后的温升是否影响正常运转,如有影响,必须用规定的介质进行设计负荷试运转。
12.0风机试运转前应符合下列要求:
12.1 润滑油的名称、型号、主要性能和加注的数量应符合设备技术文件的规定;
12.2 按设备技术文件的规定将润滑系统、密封系统进行彻底冲洗;
12.3鼓风机和压缩机的循环供油系统的连锁装置、防飞动装置、轴位移警报装置、密封系统的边锁装置、水路系统调节装置、阀件和仪表等均应灵敏可靠,并符合设备技术文件的规定。
12.4 电动机或汽轮机、燃气轮机的转向应与风机的转向相符;
12.5 盘动风机转子时,应无卡住和磨擦现象;
12.6 阀件和附属装置应处于风机运转时负荷最小的位置;
12.7机组中各单元设备均应按设备技术文件的规定进行单机试运转。
12.8 检查各项安全措施。
13.0风机在额定转速下试运转时,应根据风机在使用上的特点和使用地点的海拔高度,按设备技术文件确定所需的时间,无规定时,在一般情况下可按下列规定:
13.1 离心、轴流通风机,不应少于2小时;
13.2 罗茨、叶氏式鼓风机在实际工作压力下,不应少于4小时;
13.3 离心鼓引风机,最小负荷下(即机械运转)不应少于8小时,设计负荷下连续运转不应少于24小时;
13.4 风机不得在喘振动区域运转(喘振流量范围由设备技术文件注明)。
14.0风机运转时,应符合下列要求:
14.1风机运转时,以电动机带动的风机均应经一次起动立即停止运转的试验,并检查转子与机壳等确无磨擦和不正常声响后,方得继续运转(汽轮机、燃气轮机带动的风机的起劝应按设备技术文件规定执行)。
14.2 风机起动后,不得在临界转速附近停留(临界转速由设备技术文件注明)。
14.3 风机起动时,润滑油的温度般不应低于25℃。运转中的轴承进油温度一般不应高于40℃,再停止油泵工作;
14.4 有起动油泵的机组,应在风机起动前开动起动油泵,待主油泵供油正常后才能停止起动油泵;风机停止运转前,应先开动起动油泵,风机停止转动后应待轴承回油温度降到45℃后再停止起动油泵;
14.5 风机运转达额定转速后,应将风机调整到最小负荷(罗茨、叶氏式鼓风机除外)进行机械运转至规定的时间;然后逐步调整到设计负荷下检查原动机是否超过额定负荷,如无异常现象则继续运转至所规定的时间为止;
14.6 高位油箱的安装高度,以轴承中分面为基准面,距此向上不应低于5米。
14.7 风机的润滑油冷却系统中的冷却水压力必须低于油压。
14.8 风机运转时,轴承润滑油进口处油压应符合设备技术文件的规定,无规定时,一般进油压力应为0.08~1.15MPa高速经载轴承油压低于0.07MPa时应报警,低于0.05MPa应停车,低速运转时轴承油压低于0.05MPa时应报警,低于0.03MPa时应停车。当油压下降到上述数值时的上限时,应立即开动起动油泵或备伯油泵,同时查明油压不足的原因,并设法消除。
14.9 风机运转时轴承的径向振幅应符合设备技术文件的规定。无规定时应符合表-2-2、-2-3的规定;
表-2-2:离心轴流通风机、罗茨、叶氏式鼓风机轴承径向振动(双向)
转速
转/分<375 >375~550 >550~750 >750~1000 >1000~1450 >1450~3000 >3000 振幅不应超过㎜ 0.18 0.15 0.12 0.10 0.08 0.06 0.04
转速
转/分<3000 >3000~6500 >6500~10000 >10000~18000 主机轴承振幅不应超过(㎜) 滚动 0.06 滑动 0.50 0.04 0.03 0.02 增速器轴承振幅不应超过(㎜) 0.04 0.04 0.03
15.1泵就位前应作下列复查:
15.1.1基础的尺寸、位置、标高应符合设计要求;
15.1.2设备不应有缺件,损坏和锈蚀等情况,管口保护物和堵盖应完好。
15.1.3盘平应灵活,无阻滞,卡住现象,无异常声音。
15.2出厂时已装配,调试完善的部分不应随意拆卸。确需拆卸时,应会同有关部门研究后进行,拆卸和复装应按设备技术文件的规定进行。
15.3泵的打平应符合下列要求
15.3.1卧式和立式泵的纵、横向不平度不应超过0.1/1000;测量时,应以加工面为准。
15.3.2小型整体安装的泵,不应有明显的偏斜。
15.4泵的找正应符合下列要求:
15.4.1主动轴与纵动轴以联轴节连接时。两轴的不同轴度,两半联轴节端面的间隙应符合设备技术文件的规定。
15.4.2主动轴与从动轴以皮带连接时,两轴的不平行度两轮的偏移应符合TJ231的通用规定。
15.4.3原动机与泵(或变速器)连接前,应先单独试验原动机的转向,确认无误后再连接。
15.4.4主动轴与从动轴找正、连接后,应盘车检查是否灵活。
15.4.5泵与管路连接后,应复校找正情况,如由于与管路连接而不正常时,应调整管路。
15.5找平应以水平中开面、轴的外伸部分、底座的水平加工面等为基准进行测量。
15.6对于非中心支承的原动机如汽轮机或输送高温液体的泵(如锅炉给水泵、热油泵等),在常温状态下找正的,应计及工作状态下轴心线位置的变化。
15.7起动前,平衡盘冷却水管路应畅通,泵和吸入管路必须充满输送液体,排尽空气,不得在无液体情况下起动;自吸泵的吸入管路不需充满液体。
15.8输送高、低温液体的泵,起动前必须按设备技术文件的规定进行预热或预冷。离心泵不应在出口阀门全闭的情况下长时间运转;也不应在性能曲线中驼峰处运转。
15.9管道泵和其他直联泵(电动机与泵同轴的泵)的转向应用点动方法检查。
15.9.1屏蔽泵的转向应用下述方法检查:泵起动后,如泵的实际关死扬程与性能曲线规定的关死扬程相符,表示转向无误;如相差太大,且确认并非由于泵内(包括屏蔽电机内)气体未排尽而引起,则表示转向有误。
15.9.2水泵涡轮机组中的涡轮机的安装要求可参照同类型离心泵的规定执行。
15.9.3水泵涡轮机组试运转时,当涡轮机尚未回收能量前,应确保电动机的电流小于额定值时,严防电机超载。
16.0螺旋出碴机安装
16.1先将出碴机从安装孔斜放在基础坑内。
16.2将漏灰接口安装在锅炉底板下部。
16.3安装锥形碴斗,上好碴斗与炉体的螺栓后,再将漏灰板与碴斗的连接螺栓上好。
16.4吊起出碴机的筒体与锥形碴斗连接好。锥形碴斗的长方形法兰与筒体长方形法兰之间一定要加橡校垫或油浸扭制石棉盘根,不得漏水。
16.5安装出碴机的吊耳和轴承底座:在安装轴承座时,要使螺旋轴保持同心或一条直线。
16.6把安全离合器的弹簧调正,用扳手,扳转蜗杆方身使螺旋轴转动灵活。油箱内应加入符合要求的机械油。
16.7安妥后接通电源和水源,检查旋转方向是否正确,离合器的弹簧是否跳运,冷态试车2小时,应无异常声音和不得漏水为合格,应作好试车记录。
17.0电气开关箱安装
17.1开关箱的四条地脚螺栓(M12×220)的位置要正确,灌注要牢固,开关箱安装时要找平找正。
17.2开关箱安装好后,可敷设开关箱到各个附机电机的配管和导线,开关箱及电气设备外壳应有良好的保护接地,待各个附机安装完毕,最后接通电源。
18.0省煤器的安装
18.1快装锅炉的省煤器均为整体组件出厂,因此安装时比较简单。
安装前要认真检查省煤器管周围嵌填的石棉绳是否严密牢固,外壳箱板是否平整,有无损坏,无问题后方可进行安装。
18.2省煤器支架安装
将支架上好地脚螺栓放在基础上,当烟管为现场制作时,支架可按基础图找平找正;当烟管为成品组件时,应等省煤器就位后,按照实际烟管位置尺寸找平找正。
18.3省煤器安装
18.3.1省煤器安装前应水压试验,试验压力为1.25P+0.5MPa,p为锅炉的工作压力,无渗漏再进行安装。同时可以进行省煤器的安全阀的调整。省煤器安全阀的开启压力应为装置点工作压力的1.1倍,或为锅炉工作压力的1.1倍。
18.3.2用三木搭或其它吊装设备将省煤器安放在支架上,并检查省煤器的进口位置。标高是否与锅炉烟气出口相符;以及两口距离和螺栓孔是否相符,通过调整支架的位置和标高达到烟管的安装要求。
18.3.3一切妥当后可将省煤器下部的槽钢与支架板焊在一起。
18.3.4灌注混凝土
支架的位置和标高找正好后灌注砼。砼的标号应比基础标号高一级,应捣实和养护。
18.3.5当砼的强度达到75%时可将地脚螺栓坚固。
19.0液压传动装置的安装
19.1对预埋板应进行清理和除锈。
19.2检查和调整使绞链架纵横中心线与滑轨纵横中心线相符,以确保有大的调节量,并将铰链架的固定螺栓稍加紧固。
19.3把活塞全部提出(最大行程),并将活塞杆的长拉脚与摆轮连接好,再把活塞缸与绞链架连接好。然后根据摆轮的位置和图纸的要求把滑轨的位置找好、焊牢,最后再认真调整一下铰链架的位置并把螺栓坚固。
19.4液压箱的安装
油压箱只需按设计位置放好即好,油箱内要清洗干净,经加油器,向油箱内加入冬天10号夏天20号机械油。
19.5地下油管安装:
地下油管采用∮22×3.5的无缝管,在现场煨弯和焊接管接头,钢管内要除锈拉干净。
19.6高压软管安装
高压软管应安装在油缸与地下油管之间。安装高压软管时,应将丝头和管接头内的铁屑毛刺清除干净,避免损坏油缸和油泵。丝头连接处应用聚乙四氟乙烯薄膜或麻丝白铅油作填料,将高压软管上好。
19.7高压铜管安装
先将铜管截以适当长度,然后退火煨弯,用扩口工具扩口,再把管接头分别上在油箱和地下油管的管口上,最后把铜管上好。
19.8电气部分安装
先将行程开关架和行程撞块安好,再安装行程开关。上行程开关的位置应定在摆轮拨爪略超过刺轮槽为宜,下行程开关的位置应定在能使炉排前进80mm或活塞不得到缸底为宜。最后进行电气配管、空线、压线及油泵电机接线。
19.9油管路的冲洗和试压
把高压软管与油缸相接一端御开放在空油筒内,然后起动油泵调节溢流阀调压手轮,顺时针旋转使油压维持在0.2MPa,再通过人工方法控制行程开关使油能对两条管进行冲洗。冲洗时间为15~20分钟,每条油管至少冲洗2~3次。冲洗完毕后将高压软管与油缸连好。
油管试压,利用液压箱的油泵即可,起动油泵通过调压手轮使油压逐步升至3M Pa,在此压力下活塞动作一个行程,油管及接头油缸不漏为合格,立即将油压调到炉排工作压力,因油泵不得长时间超载,1~2t/h链条炉排油压为1.2MPa;4t/h链条炉炉排油压为1.5M Pa。
19.9.1摆动内部应擦洗后加入适量的20#机油。
19.9.2液压传动装置充洗试压时应作好记录。
20.0除尘器的安装
20.1除尘器支架安装
将地脚螺栓安装在支架上,然后把支架安在基础上。
20.2安装除尘器
支架安装好后,吊装除尘器,上好除尘器与支架的连接螺栓,吊装除尘器时不得损坏内部的耐磨涂料。
20.3安装烟管
先从省煤器的出口或锅炉后烟箱的出口安装烟管在与除尘器的扩散烟管连接时用∮10的石棉扭绳作填料,连接要严密、烟管和扩散管安装好后检查扩散的法兰与除尘器的进口法兰位置是否合适,如略有不合适时可适当调整除尘器支架的位置和标高,使除尘器与烟管达到妥善连接。
20.4检查除尘器的垂直度
除尘器和烟管安装好以后,检查除尘器及支架的垂直度和水平度,除尘器的垂直度为1/1000,然后将地脚螺栓灌注混凝土。待砼的强度达到75%时将地脚螺栓坚固。
20.5安装锁气器
锁气器是除尘器的重要部件;是保障除尘器效果的关键部位之一。因此锁气器的连接要紧密,舌形板接触要严密,配合要合适。
20.6现场制作烟管时除尘器的安装方法
当除尘器至省煤器或除尘器至锅炉的烟管在现场制作时,除尘器应按基础图安装即可,最后安装烟管。
当在现场制作除尘器的扩散管时,扩散管的渐扩角不得大于20 度。如图所示:
21.1每节烟囱之间用¢8石棉绳作密封填料,连接应严密牢固,并保证直线度。
21.2当烟囱高度超过建筑物时必须安装避雷针。
21.3烟囱在适当高度处需安装拉线,不少于3根,拉线宜用钢丝绳;拉线的固定装置应牢固,分布均匀,在离地适当高度安装绝缘球,不宜低于3米。
21.4用吊装设备把烟囱吊装到位,调整垂直度,控制垂直度不超过1 ㎜/m,且全高不超过20㎜,最后拉紧拉线紧固基础螺栓;调整拉线使之受力均匀、合理。